Solderability is Defined as the Ability of a Metal to Be Wetted by Molten Solder
Measurement of solderability can be done several ways. A Wetting Balance measures and records the wetting force as a function of time. While this is a quantitative test, it presents complications when relating the results to actual soldering practice. Additionally, it requires an expensive piece of laboratory equipment.
A frequently employed qualitative test is the solder bath dip and look test. This test employs a dipping mechanism, a solder pot, a low power microscope, and may include requirements for steam aging of the test samples. The procedure for using this test for the solderability of wire is well defined in American National Standards ANSI/J-STD-002 as well as MIL-STD 202/208F.
The solder bath dip and look test can be done on bare or plated surfaces. On bare surfaces the test is a general indicator of surface cleanliness and oxides. On plated surfaces the test is a good indicator of the solderability of the plated wire when in service. Steam aging the plated samples promotes degradation by both intermetallic growth and surface oxidation for subsequent evaluation with the dip and look test. The general dip and look solderability acceptance criteria for the tested area is 95% wetting coverage whether initially steam aged or not.
Definitions
Wetting:
The formation of a relatively uniform, unbroken and adherent film of solder to a base metal.
Dewetting:
Molten solder coats a surface and then recedes to leave irregularly shaped mounds of solder separated by areas covered with a thin film of solder and not exposing the base metal.
Non-wetting:
The partial adherence of molten solder to a surface leaving the base metal exposed.
Pin Holes:
Imperfections in the wetted surface appearing as small holes that penetrate thru to the base metal.
Shelf Life:
The period of time, usually measured in months and commencing with the plating date of the wire, that the wire will pass a solderability test.
Steam Age Categories
The ANSI/J-STD-002 solderability test recognizes three steam aging categories.
Category 1
- No Steam Aging Requirements
- Minimum Coating Durability
- Intended for surfaces which will be soldered within a short period of time (e.g., up to 6 months) from the time of testing and are likely to be exposed to a minimum of thermal exposure.
Category 2
- 1 Hour +/- 5 min. Steam Aging
- Typical Coating Durability (for non-tin and tin-lead finishes)
- Intended for surfaces finished with other than Sn or Sn/Pb coatings which will be soldered after an extended time from the time of testing and which may see limited thermal exposure prior to soldering.
Category 3
- 8 Hours +/- 15 min. Steam Aging
- Typical Coating Durability (default for tin and tin-lead finishes)
- Intended for surfaces finished with Sn or Sn/Pb coatings which will be soldered after an extended storage (e.g. greater than 4 months) from the time of testing and/or which see multiple thermal exposures prior to soldering.
Shelf Life
The correlation between steam aging and natural aging has, in controlled environments, shown that properly plated tin and tin/lead systems that pass solderability when steam aged for 8 hours will, when naturally aged, continue to solder 12 months later and may continue to solder beyond that time. However, due to the combined effects of the variables of alloy base metal, underplates, surface geometry and storage environments, it is not possible to accurately predict the maximum storage life of any plated wire. Maximizing solderability shelf-life of plated copper alloy wire is to:
- Use an underplate of nickel (preferred) or copper under the tin or tin-lead plating.
- Avoid tin or tin-lead finishes made “bright” by the use of chemical or organic additives.
- Store the wire as packaged, preferably in a climate controlled environment.
Solderability Coverage Guide
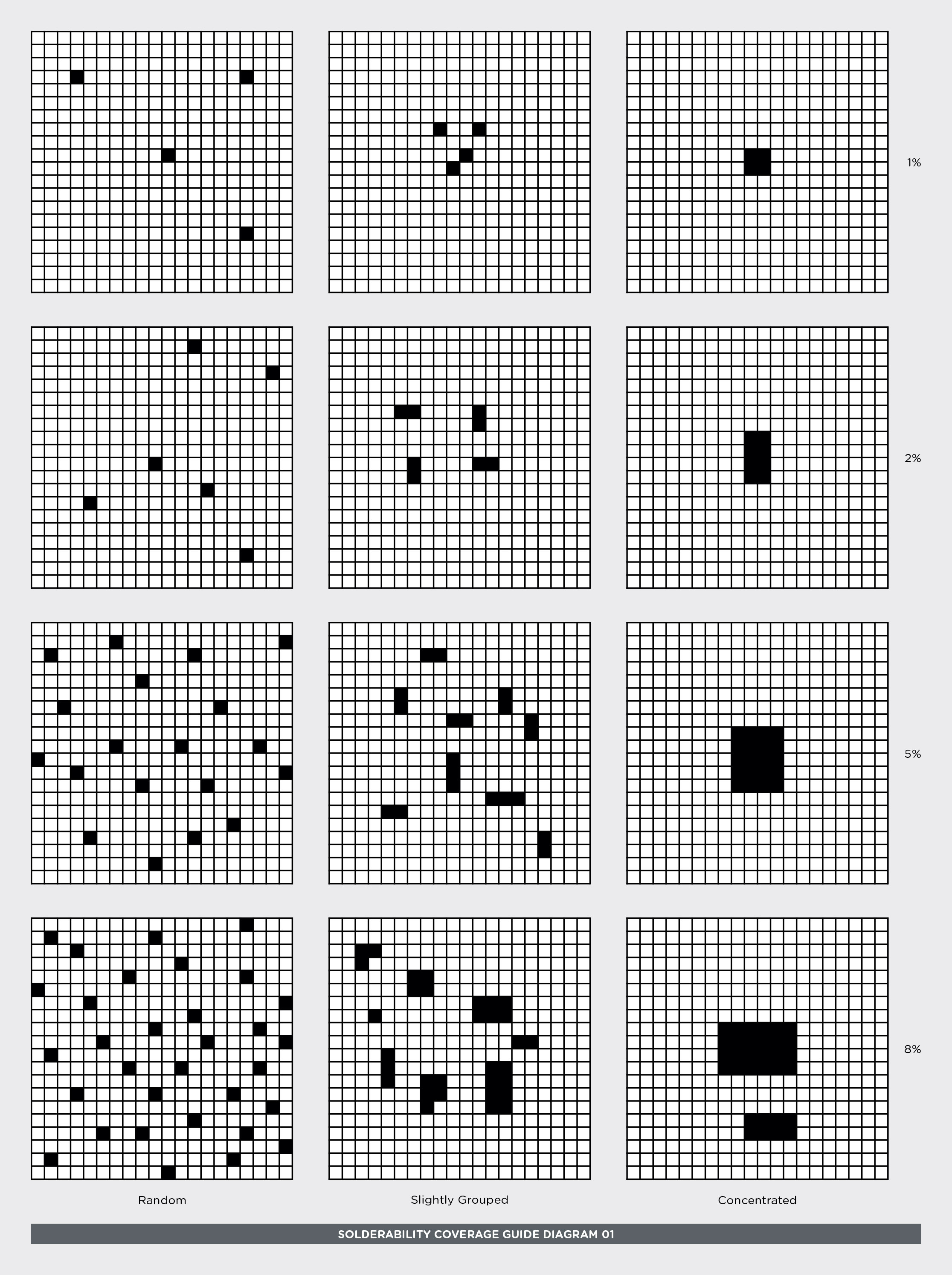
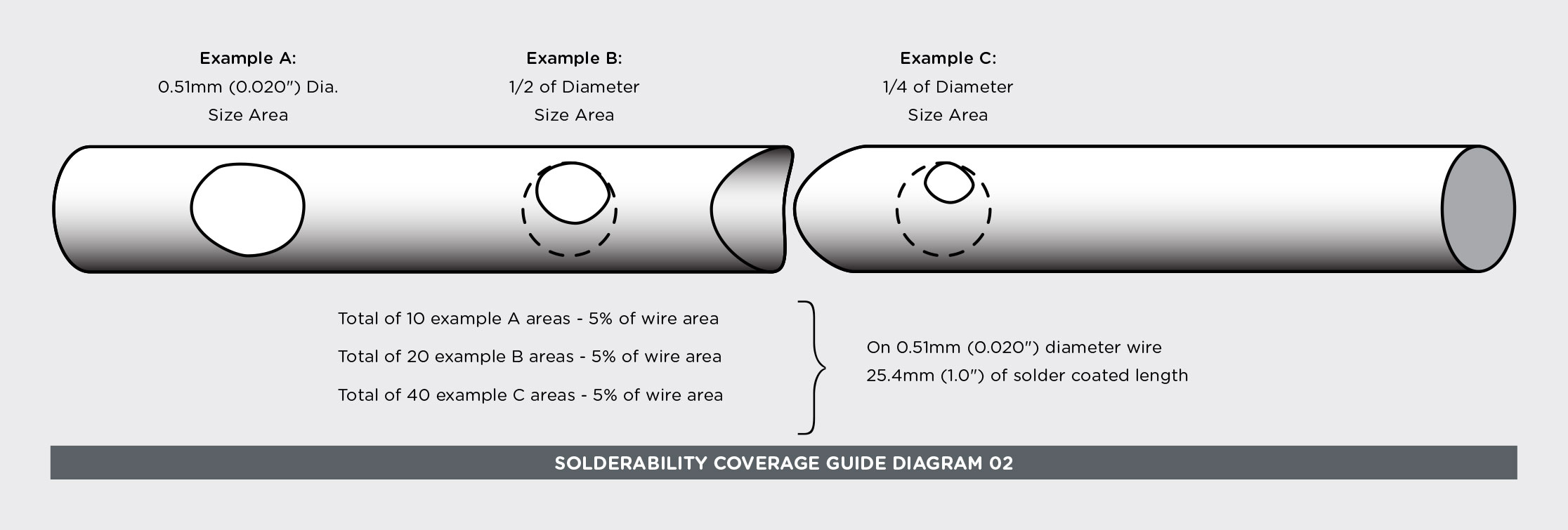